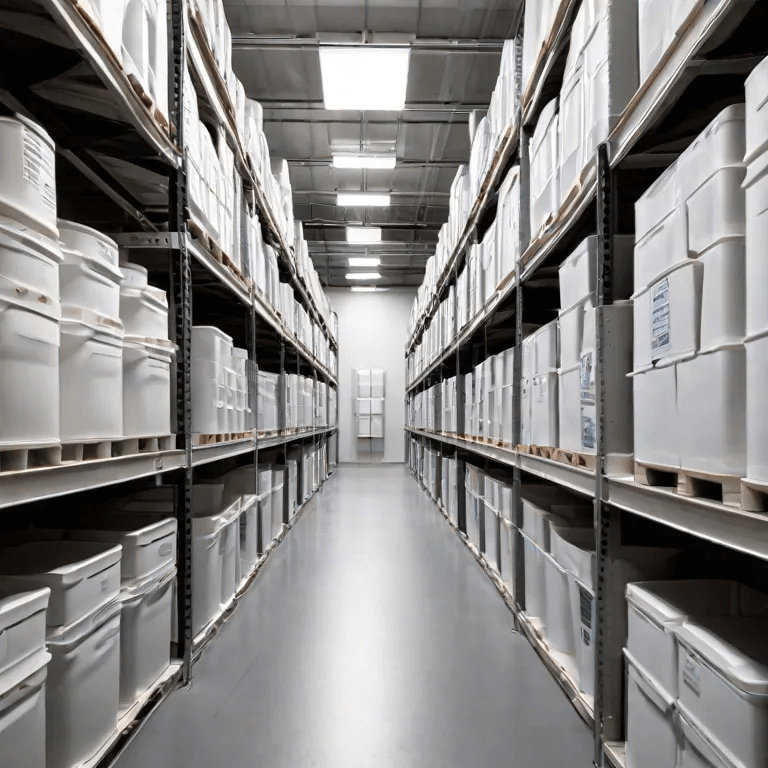
Excipients, the inactive ingredients in pharmaceutical formulations, play a crucial role in ensuring the safety, efficacy, and stability of drugs. Proper storage conditions are essential to maintain the quality and integrity of these materials throughout their lifecycle. Failure to adhere to best practices can lead to degradation, contamination, or compromised performance, ultimately impacting the final drug product.
Understanding Excipient Stability
Excipients can be susceptible to various environmental factors that can affect their stability. Moisture, oxygen, temperature fluctuations, and light exposure are common culprits that can trigger chemical or physical changes, potentially altering the excipient’s properties and performance.[1]
“Stability issues occur more frequently from exposure to moisture or oxygen rather than temperature extremes.” – Ian Silverstein, Pharmaceutical Technology Europe
To mitigate these risks, excipient manufacturers and pharmaceutical companies must implement robust stability testing programs. These programs involve subjecting excipients to controlled conditions that simulate real-world storage and transportation scenarios, allowing for the identification of potential degradation pathways and the establishment of appropriate shelf-life and storage requirements.[2]
Packaging and Tamper-Resistance
Proper packaging is a critical line of defense against environmental threats and potential tampering. Excipient suppliers should provide evidence of the suitability of their packaging materials to protect against moisture and oxygen ingress.[1] High-density polyethylene (HDPE) drums, for instance, offer superior resistance to tampering compared to fiber drums or bags.
Tamper-evident seals, unique to the excipient manufacturer, are essential for ensuring the integrity of the packaging. These seals must be designed to break upon opening, preventing reapplication and indicating potential tampering.[1] Incoming inspections by pharmaceutical firms should verify the authenticity of these seals against reference samples provided by the supplier.
Storage Conditions and Monitoring
Excipients should be stored in suitable containers under appropriate conditions, as specified by the manufacturer. Where special storage requirements exist, such as temperature or humidity control, these conditions must be provided, monitored, and recorded.[3]
Environmental monitoring systems play a crucial role in ensuring compliance with storage conditions. Temperature and humidity sensors, coupled with data logging and alarm systems, can alert personnel to deviations, enabling prompt corrective actions.
Segregation and Traceability
Proper segregation of excipients is essential to prevent cross-contamination and mix-ups. Dedicated storage areas, clearly labeled and separated based on material grade, batch, or quarantine status, should be established.[4] Electronic inventory management systems can further enhance segregation and traceability, provided they are properly validated and maintained.
Distribution records must be detailed enough to facilitate traceability in the event of a recall. Excipients should be transported under the conditions specified on the labels, with their identity and batch information maintained throughout the supply chain.[3]
Continuous Improvement and Quality Management
Excipient manufacturers and distributors should adopt a continuous improvement philosophy, regularly reviewing root causes of non-conformances, quality complaints, and audit findings to identify opportunities for enhancement.[3] Implementing a robust quality management system, aligned with Good Manufacturing Practices (GMP) and industry guidelines, is crucial for ensuring consistent excipient quality and mitigating risks.
In conclusion, proper excipient storage practices are essential for maintaining the integrity and performance of pharmaceutical products. By adhering to best practices in packaging, storage conditions, segregation, traceability, and continuous improvement, manufacturers and distributors can safeguard the quality of these critical materials, ultimately contributing to patient safety and drug efficacy.
References:
[1] Silverstein, I. (2016). Excipient Quality and Selection. Pharmaceutical Technology Europe, 28(2), 16-20.
[2] International Pharmaceutical Excipients Council (IPEC). (2022). Excipient Stability Guide.
[3] World Health Organization (WHO). (2023). Good Manufacturing Practices for Excipients Used in Pharmaceutical Products.
[4] International Pharmaceutical Excipients Council (IPEC). (2021). Good Distribution Practices Audit Guide for Pharmaceutical Excipients.